(Cut Make Trim) CMT process flow diagram
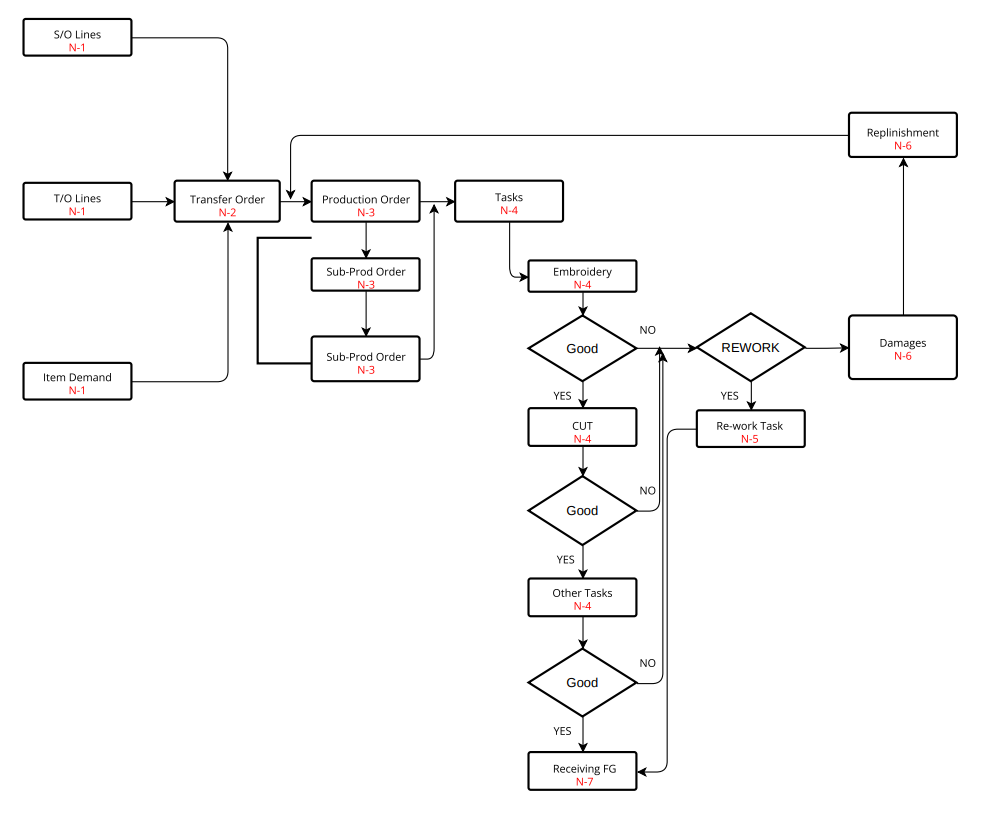
The diagram above is the visual representation of the ‘standard’ cut-make-trim solution that Folio3 offers in its NStitch Solution for AFA. By standard we mean the basic, bare minimum cmt solution that is built on top of the native functionalities of NetSuite and which is required to perform the complete apparel life-cycle. It includes different nodes, represented as N1, N2, N3 and so on. These represent the different stages of the CMT process.
The Staging Screen (N1)
A staging screen is created by the Folio3 team. It is a suitelet which renders a Vue JS app. The UI is quite user-friendly and allows the users to make multiple selections as per their ease.
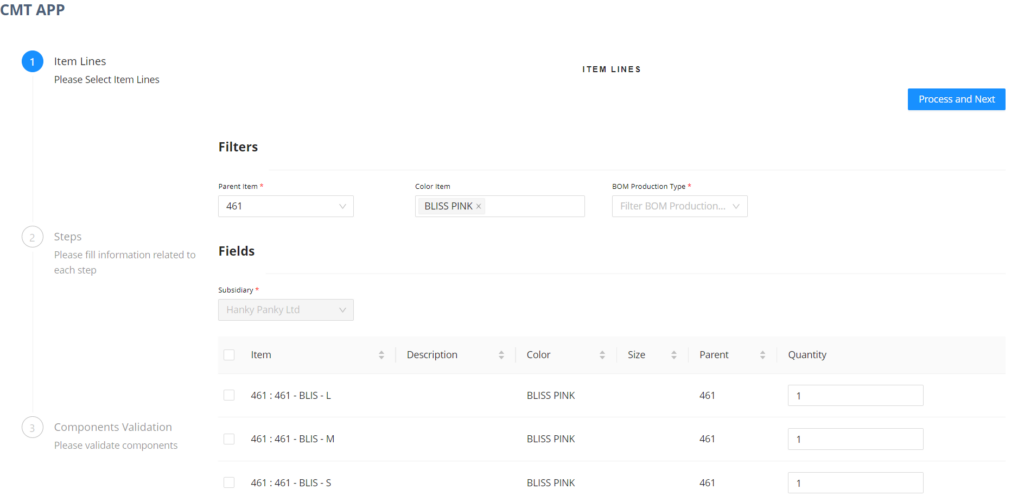
This staging screen contains multiple filters and fields to drill down on line items (items to produce). These items to produce are usually Assembly type Matrix SubItems with color and/or size defined. The main filters include a parent item filter which fetches all the variants of the item. Number of rows can be filtered even further by selecting colors available against this parent item. The quantity required to be produced is editable. The subsidiary is pre-selected and is sourced from our NStitch configurations custom record.
Note: At the time of staging, line items from Sales Order and Transfer Order can also be fetched. For this purpose, relevant configuration has to be turned from cmt configurations. Additionally, any other custom criteria can be set as per client requirement. You guessed it right, in NStitch configurations.
After some of the lines are selected, next comes the steps required in the NStitch CMT process. These steps are sourced from the item’s (or line items in the case of SO/TO) bill of material (BOM). For every step, there is an option to get it done in-house or out-source it to a vendor. If the process is to be done inhouse then location becomes mandatory and if a certain cmt process needs to be outsourced to a vendor then selection of vendor becomes essential. After confirming the steps, the user can proceed to the components validation screen.
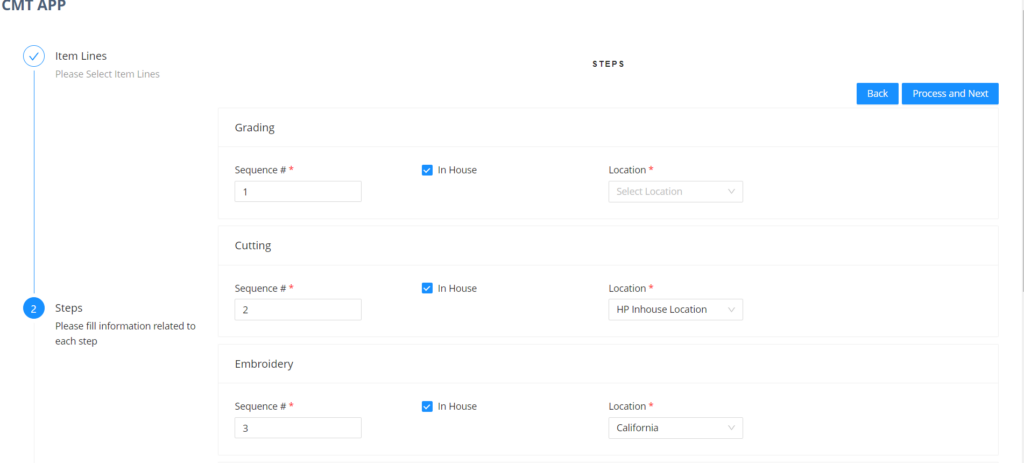
Note: Folio3’s NStitch solution is a data sensitive solution. This means that if data related prerequisites are not fulfilled then it won’t work. (Prerequisites will be covered in a separate blog).
Next step is the validation of components. Components are the inventory and service type items required to get a particular step done. Referring to the image below, Service item 2 is one of the service components of step ‘Grading’. System allows users to edit the required quantity for components. When all the components of all the steps are validated, the user can proceed to creation of a production order / cut-order.
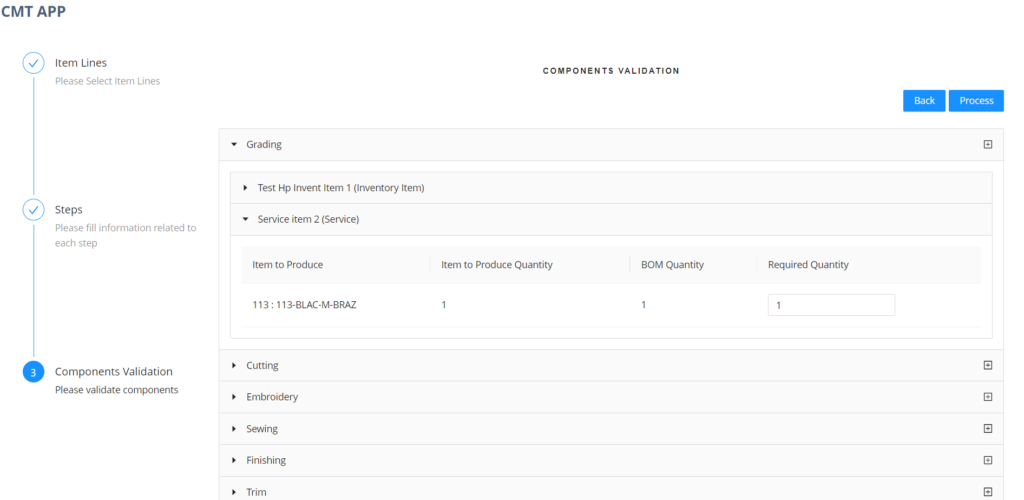
Transfer Orders (N2)
After the user submits the information they selected on the staging screen, the system triggers a background job (which means users can proceed with some other task or can wait for the script to end). This background job does multiple tasks including the creation of the production order. One of the tasks it does is to create transfer orders (one TO for each step). The purpose of this TO is to transfer inventory for components (inventory type) from a warehouse location to vendor location (if the task is out-sourced). For in-house, TOs are not created.
Production Order (N3)
The background job is responsible for creating the production order (or cut order). I will be using the term production order for the rest of this blog. The production order created by Folio3’s cmt solution is a custom record which consists of multiple (child) sub-records, such as Tasks, Items to Produce, BOM, Sub-Assembly Production Orders etc. Along with these subrecords, there are numerous body-level fields which enhance the visibility of end users, such as Style (Parent Item), Subsidiary, Completion percentage etc. A production order consists of items to produce belonging to a particular parent item. Two different items cannot be grouped together.
- Tasks are the same steps being sourced from the staging screen.
- Items to produce are the actual items being produced via production order.
- Sub-Assembly production order is similar to the actual or parent production order except that it is created whenever there is an assembly type component present in the bill of materials (BOM).
- BOM components is the list of all components (service, inventory and service) belonging to every item to produce.
The image below illustrates the skeleton of a production order.

Tasks (N4)
Next step is the actual execution of the production order. A NStitch CMT Task can be processed in the following ways:
- Creation of Service Purchase Order to record service charges (to perform a particular task). It is worth reiterating that a service PO is created only when a task is out-sourced. For in-house tasks, a simple journal entry is created to record expenses.
- Second step is to record consumption of components. Here, the user selects the required components (inventory type), define the required bom quantity to consume and system records consumption by creating a negative inventory adjustment (adjustment quantity is set to negative to deplete the inventory).
The same process is repeated for other tasks as well until all the steps are completed. This solution gives a warning if a particular task is not completed and a new task is started. E.g. Embroidery is started before cutting is completed. This check is put in place to ensure sequential execution of tasks as is the case with many apparel industries.
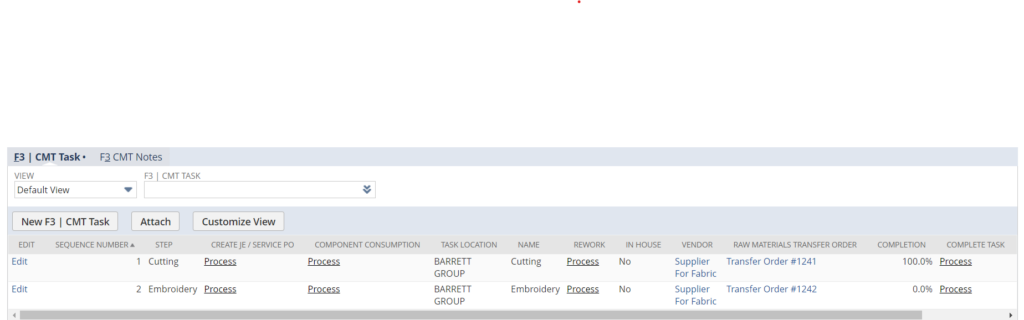
Rework Task (N5)
There is a rework link available on every task. This is an added feature in Folio3’s NStitch solution which allows companies to re-do a particular task should any issue arise with that task. Pressing hyperlink ‘Process’ under the Rework column will create a replica task with the same items to produce and the BOM component. All the processes can be carried out as defined in the N4 section.
Damages and Replenishment (N6)
Folio3 NStitch solution also has an add-on feature which can be enabled via configuration. This feature allows damages to be recorded against a particular item to produce. For example, an item to produce gets reduced in quantity after cutting is done. Out of total production of 10 such units, 2 got damaged. This solution has the capability to record this damage and also reduce the quantity being passed on to next stages as well, such as embroidery such that only 8 units are available for embroidery. To make up for those 2 units lost, this well-thought solution also has the ability to replenish. For this purpose, a sub-production order for 2 units(quantity) is created for the item to produce which got damaged.
Receiving (N7)
The final step in the CMT process is to receive (increase the inventory of) items to produce after they have gone through the complete steps/tasks. System increases the inventory of such items and creates an inventory adjustment to do so.
The screenshot below shows this process.
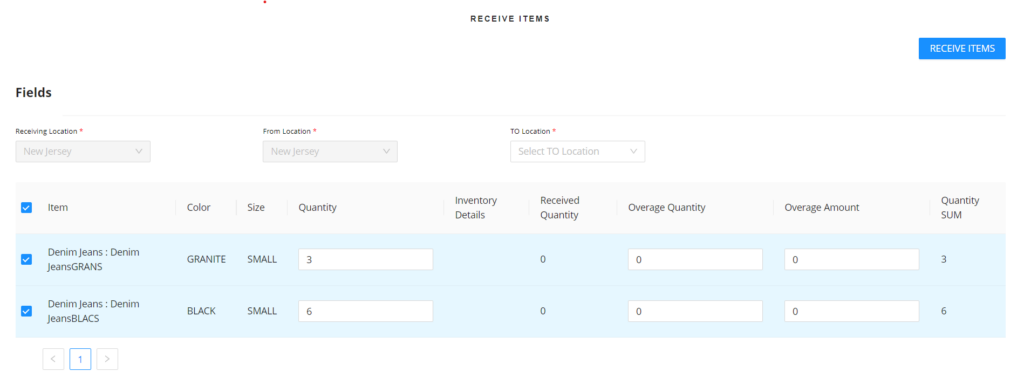
Conclusion:
Folio3’s NStitch solution is a one-stop solution for managing your apparel business. It not only manages your inventory, but also takes care of costing. The solution also has customized reports which enhances the visibility of the process. The reports vary from customer to customer but there are some generic reports such as service PO, open order report etc. The next blog will be on data prerequisites for CMT.
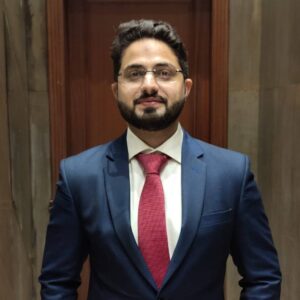
About the Author
Usman Majied
Senior Software Engineer - Folio3
Usman Majied is a tech enthusiast who loves challenges and is eager to learn new technologies. He is interested in reading books, and esports and strives to stay fit.